Tired of Deferred Maintenance? Here’s How to Reduce It at Your Facility
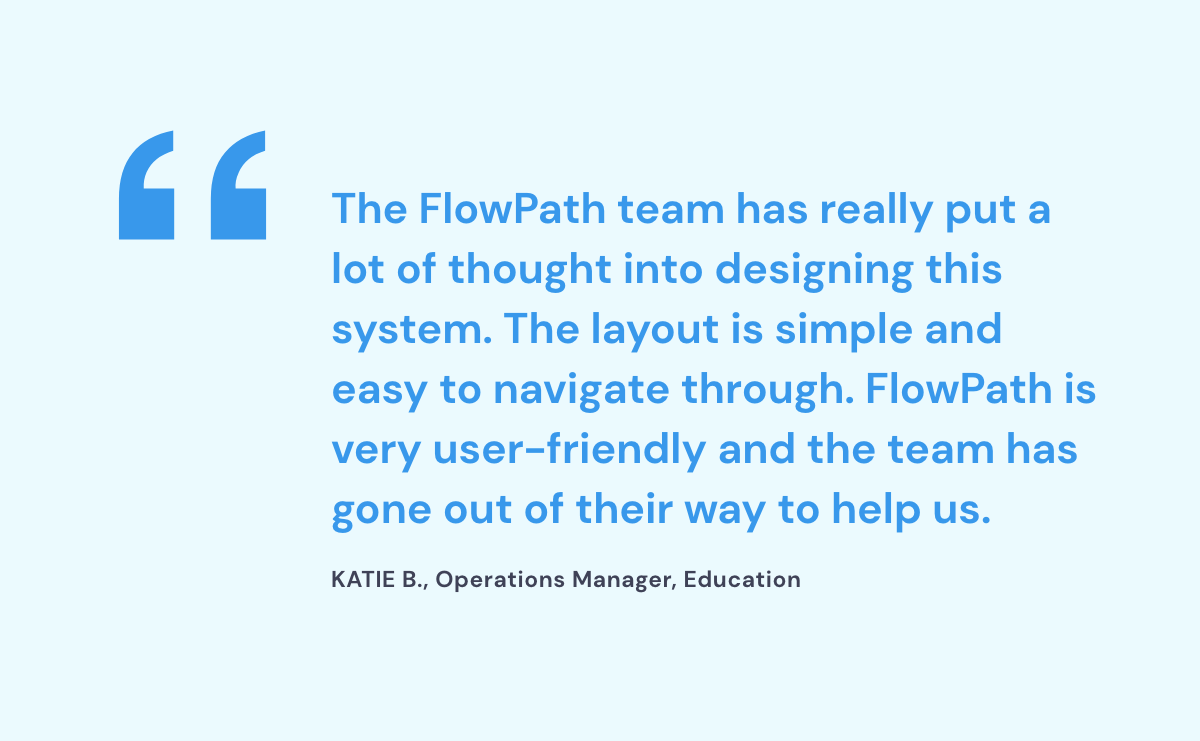
“I like dealing with deferred maintenance,” said no facility manager ever.
Regardless of the type of facility you manage, chances are you’ve dealt with deferred maintenance at one time or another, if not on a regular basis. And it’s not a new problem, either. In fact, the costs and dangers of postponed upkeep have plagued facilities for decades.
In higher education, for example, the burden of deferred maintenance began affecting many institutions in the 1970s. Following World War II, college enrollment grew at a rapid pace. In order to accommodate the burgeoning student population, colleges began opening at “a rate of one every two weeks from 1955 to 1974.” As those facilities began to age, it was only a matter of time before administrators realized they had a huge problem on their hands: deteriorating assets that were too expensive to fix due to a multitude of roadblocks like rising costs, budget reductions, and inadequate funding.
While deferred maintenance was born from post-WWII expansion in higher education, countless other industries—from restaurants to real estate—are faced with its challenges today. So, what’s the good news in this scenario? There are a few ways to reduce deferred maintenance at your facility. We’ll examine why deferred maintenance happens, ways to decrease it, and how to be more proactive in your approach to maintenance moving forward.
Deferred Maintenance: What’s the Deal?
Deferred maintenance is defined as any type of maintenance work that’s delayed due to a lack of resources like time, labor, and/or funding. It could involve an asset that breaks down and can’t be repaired due to budget constraints. It might be a work order that was abandoned in order to address a more urgent repair. It could involve the deterioration of the facility itself: peeling paint, parking lot potholes, and other structural repairs that are not considered high priority tasks.
Deferred maintenance often occurs because of budget or labor limitations, but the irony is, delaying repairs can be incredibly costly and even dangerous over time. As unresolved issues pile up, they can trigger more problems, leading to decreased productivity, inefficiencies, and even unsafe working conditions.
Why Deferred Maintenance Happens
While every facility manager tries to avoid the dreaded “snowball effect,” deferred maintenance remains a common occurrence. But why? Deferred maintenance can happen for any number of reasons at any type of facility. Here are a few of the most common culprits:
- Budget Constraints: It’s no secret that equipment replacement, repairs, and labor cost serious cash. Without proper funding, these tasks can quickly pile up, and limited budgets mean certain issues will always take priority over others. It could also lead to “cutting corners” in order to execute those tasks in more cost-efficient ways, ultimately leading to even more issues down the line.
- Lack of Preventive Maintenance: Also known as routine maintenance, preventive maintenance involves inspecting equipment and assets on a regular basis with the goal of keeping them in working order. It’s an effective strategy, yet many facilities lack preventive maintenance plans, or their existing strategies are inadequate. Instead, reactive maintenance or even emergency maintenance is performed instead, which inevitably leads to deferred maintenance.
- Insufficient Labor and/or Skillsets: Maybe you don’t have enough maintenance personnel to handle repairs. Maybe your team is overloaded with work orders and can’t keep up. Maybe workers lack the skillset to complete certain repairs, but the budget can’t accommodate hiring an outside contractor. All of the above means certain maintenance issues can fall to the back burner.
- Lack of Tools & Documentation: If you don’t have the right tools, you simply can’t get the job done—and that includes documentation tools, too. Without the right systems in place, it becomes incredibly difficult to manage and execute maintenance-related tasks and backlogged work can quickly spiral out of control.
Often, these roadblocks are beyond the control of a facility manager. Nonetheless, there are certain measures one can take to mitigate the deferred maintenance cycle.
How to Decrease Overall Deferred Maintenance
Deferred maintenance doesn’t have to be a never-ending cycle of incomplete work orders. In fact, these issues can be reduced with the right strategies, tools, and planning in place. Here are a few things you can do with the help of FlowPath’s CMMS:
1. Keep track of all maintenance activity. In order to make data-driven decisions from a strategic standpoint, facility managers need a high-level view of everything: costs, resources, dates, assets. The right CMMS can help you accomplish this, making it much easier to keep tabs on what’s happening in the facility and how to strategically manage it all.
2. Implement a preventive or routine maintenance strategy. Having a solid preventive maintenance strategy can decrease the number of tasks that get moved to the backlog because of a lack of resources and budgets. Using software to keep you on track with preventative maintenance planning is huge.
Click here to learn more about the importance of routine maintenance >>
3. Automate work orders to keep tasks moving. Generating and managing work orders takes time—but there’s an easier way. By automating these tasks, facility managers can free up valuable time by seamlessly creating work orders quickly and efficiently. Users can submit orders by call, text, email, or online through their desktop, laptop, tablet, or mobile device.
4. Access important data. It’s essential to remain up-to-date on all important data in order to track overall progress and keep tabs on maintenance. Instead of manually creating reports or spreadsheets, use a CMMS like FlowPath with a customizable, interactive dashboard containing analytical information about your business and assets. Then, you can easily share that data with management to justify the need for additional cost or labor.
Decreasing Deferred Maintenance with FlowPath
If you’re ready to start decreasing deferred maintenance at your facility, we’re ready to help. FlowPath streamlines all aspects of facility management so that managing maintenance is easier and more efficient.
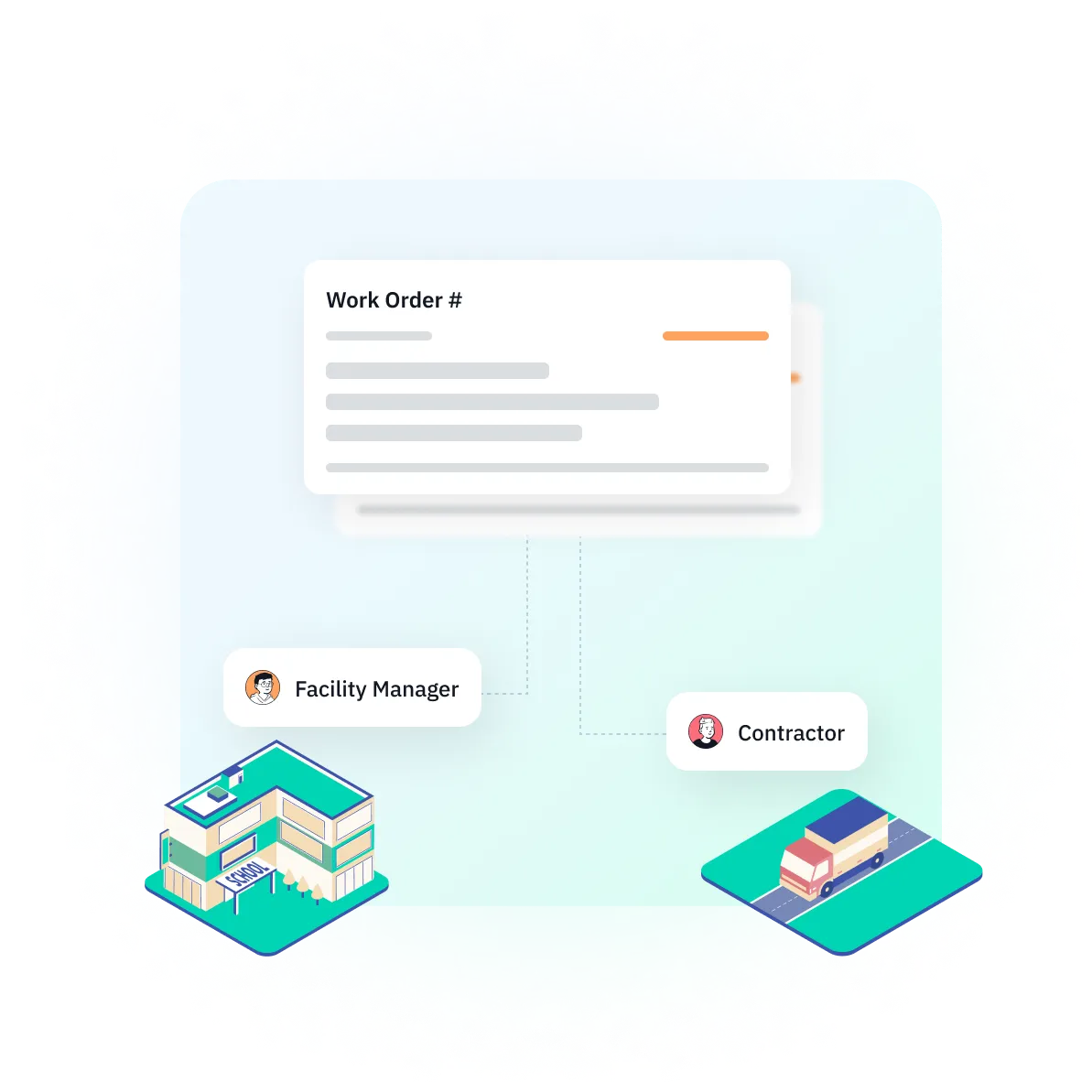
Our user-friendly interface is intuitive for all team members, consolidates the different processes, brings uniformity to previously disjointed systems, and provides easy access to important data.
Schedule a demo today to see how FlowPath can help decrease deferred maintenance at your facility.