Preventive Maintenance Plans: Here’s What You Need to Know
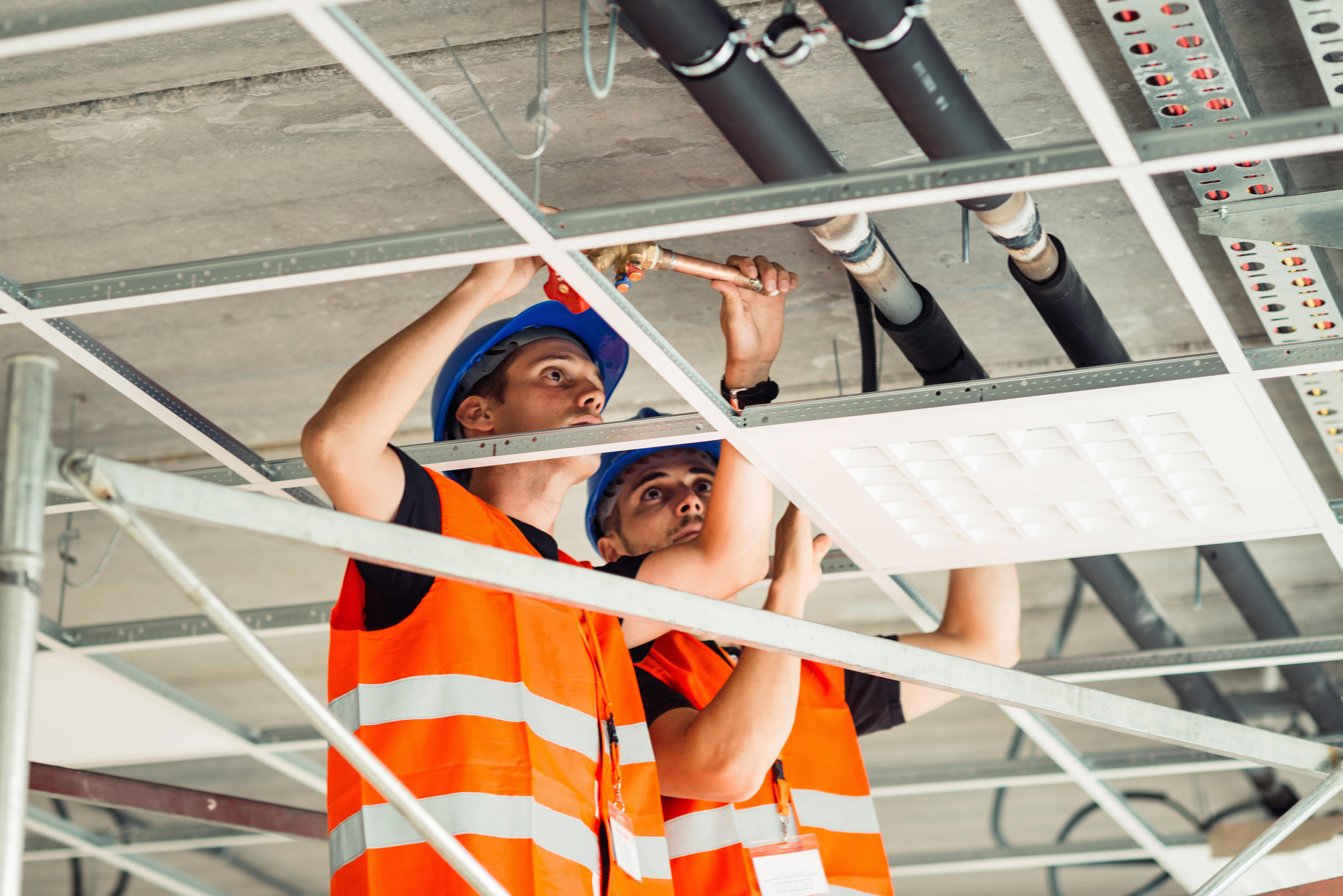
Famous last words: “If it ain’t broke, don’t fix it.”
As a facilities manager, you’ve probably heard this before. And, while this tried and true mantra works in many situations, you may want to reconsider applying it to your facility maintenance work.
This approach may work in the short term, but this could also create a pattern of constant reactive and emergency maintenance tasks. This typically results in unnecessary stress, wasted time, and thousands of dollars down the drain each year. If your team constantly finds itself resorting to reactive maintenance, it’s likely time for a change. A sound preventive maintenance plan is essential for keeping your equipment and facility operations running smoothly. Below, we’ve laid out a guide to preventive maintenance so that you can create an effective PM program of your own.
What is Preventive Maintenance?
Preventive maintenance (or preventative maintenance) is the regular and routine maintenance of equipment and assets with the aim of reducing unplanned downtime, idle time, and unexpected equipment failures.
A preventive maintenance plan is a series of processes, guidelines, and tools for conducting regular maintenance on equipment and other assets. Preventive maintenance programs can do wonders for facilities that find themselves deferring to reactive maintenance all too often.
Key Action Items of Preventive Maintenance
Preventive maintenance programs take a proactive approach towards maintenance and involve four key action items: inspection, detection, correction, and prevention. Each of these concepts is fundamental to the success of any PM program.
- Inspection: Routine inspections are an essential part of preventive maintenance. Inspections allow facility managers to ensure that equipment is safe to use, preventing workplace injuries and giving the organization an extra line of liability protection. Regular inspections also confirm that equipment is functioning properly and as the manufacturer intended, which protects your property and saves money.
- Detection: Preventive maintenance plans save facilities a significant amount of money by helping you detect problems early on, at the stage when issues are still fairly easy and inexpensive to resolve.
- Correction: PM programs encourage facility managers to take a proactive approach to equipment maintenance and correct issues before they occur. If a problem—or potential problem—is detected, facility managers know the steps they can take to promptly address these issues before they have the opportunity to severely limit or shut down operations.
- Prevention: It’s in the name! In preventive maintenance, facility managers can combine inspection records and maintenance notes to learn from the past and mitigate repeated issues. Prevention of asset and equipment failure will increase productivity and reduce stress for facility staff. If equipment works as expected, your team can be more proactive.
The Benefits of Preventive Maintenance Programs
The main purpose of preventive maintenance programs is twofold: (1) increase asset longevity and productivity and (2) keep people and assets safe.
A well-established preventive maintenance plan can help facility managers achieve various benefits, including:
- Reduced equipment depreciation
- Prevention of unexpected equipment failures
- Elimination of unnecessary inspections and maintenance tasks
- Extending assets’ useful lifespan (which saves money)
- Preparation for and prevention of future roadblocks
5 Steps for Creating a Successful Preventive Maintenance Plan
Every facility is different, so there is no true one-size-fits-all approach to creating a preventive maintenance plan. With that being said, these five steps can help you build an effective blueprint for success and will go a long way in making your facility more efficient and sustainable.
- Establish and prioritize goals
The first step to building a successful preventive maintenance plan is deciding what you plan to achieve. Each facility has its own goals which influence decisions. Maybe your focus is reducing downtime, cutting costs, or increasing reliability. Pinpoint the reasons you want to create a structured PM program and plan them out.
Once you’ve decided on your goals, you need to prioritize them. By prioritizing, you know where to focus your time and resources first. This is extremely important since you’re already busy enough as a facility manager.
- Create KPIs
With your goals now organized, you need a way to track and measure them. It can be hard to check the success of your PM program without concrete numbers. There are various maintenance metrics out there, including productivity, equipment downtime, equipment costs, and preventive maintenance efficiency. Once you’ve established which KPIs you’ll use to define success, the next step is creating a framework for tracking these metrics. It’s crucial to build processes and procedures that ensure data is collected and analyzed on a regular basis.
- Leverage the right technology
Technology is one of the main ingredients for successful preventive maintenance programs. Opting for a digital solution helps you efficiently manage preventive maintenance tasks, such as inventory management, reporting data, and scheduling work orders. If you find yourself using a legacy system, like pen and paper or excel, it’s probably about time you upgrade your workflows.
Several factors should be considered when deciding upon the right software system for your facility. Some factors to think about include the size of your facility and team, each person’s skill set, budget, asset capabilities, data security, and more. Another important aspect to consider is the ease of use. An intuitive CMMS like FlowPath can easily integrate with your current workflows and help speed up your facility processes.
- Train and implement
By this stage, you’ve established what needs to be done and how you plan to tackle it. Next, you need to effectively communicate this with the rest of your team. Creating a training strategy, including establishing standard operating procedures, will help everyone get up to speed on proper equipment maintenance. Team members also need to be onboarded to any new software tools as well.
Once everyone is familiar with your preventive maintenance program, it’s time to implement it. You can help your team adjust to a new way of doing things (especially if preventive maintenance is new at your facility) by starting small or testing your PM program at one initial site or only a few particular assets before fully embracing your new preventive maintenance plan.
- Fine-tune your plan
This step is never truly completed. Your preventive maintenance plan should constantly be under construction if you want to avoid common facility management roadblocks. Continuously work on fine-tuning your procedures and filling in the gaps that you discover along the way. You can use your KPIs to determine where your strengths and weaknesses lie. A crucial part of this phase is including all stakeholders (technicians, operations, reliability engineers, etc.) in the process of improvement. Gather feedback from anyone and everyone involved and lean heavily into maintenance software reporting.
The Bottom Line on Preventive Maintenance Programs
Creating a successful and sustainable preventive maintenance plan for your facility doesn’t just happen overnight. It is a highly involved process. With that being said, all of the work you put into building an effective PM program will save you down the line when it comes to facility efficiency and incurred costs.
A well-structured preventive maintenance program is attainable for all maintenance operations. If you’re looking to build a preventive maintenance plan for your facility, an all-in-one solution like FlowPath is your best friend. Schedule a demo today and unlock your facility’s true potential.