How to Master Maintenance Schedules with FlowPath
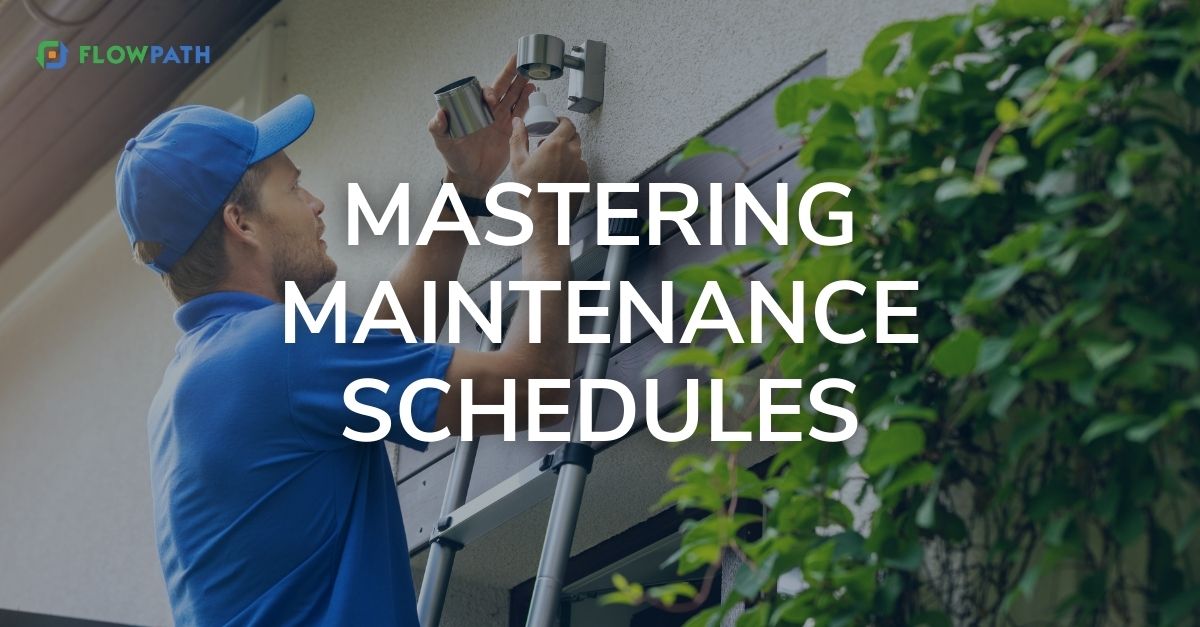
“Someone’s sitting in the shade today because someone planted a tree a long time ago.” -Warren Buffett
This quote from American business magnate Warren Buffett perfectly encapsulates the value of planning ahead. Without a clear plan, you’re bound to find yourself lost and in the weeds—especially when it comes to facility management. Maintenance planning and scheduling are absolute necessities and should be considered by every facility manager. In this blog, we’ll be discussing the importance of scheduled maintenance and why it should be part of your own facility operations. Your team (and future you) will thank you later.
What is Scheduled Maintenance?
An optimized facility maintenance schedule will have any facility operating at peak organization and efficiency. Scheduled maintenance is any maintenance task that takes place after a documented request, scheduling, and assignment process. Efficient maintenance scheduling requires that facility managers take many factors into consideration, including inventory status, facility operating hours, task priority, and technician availability. Your facility’s maintenance schedule may include tasks such as inspections and repairs, isolated responses to work orders, and routine maintenance.
Benefits of scheduled maintenance
Overall, the implementation of maintenance schedules can greatly increase a facility’s operational efficiency and profitability. Scheduled maintenance will reduce equipment breakdowns and unexpected downtime while simultaneously increasing productivity and asset life expectancy.
Workplace safety can also be bolstered by equipment maintenance scheduling and planning. Assets and equipment are better maintained and less likely to experience issues and disruptions when their regular maintenance is built into a facility’s standard operations.
Implementing maintenance schedules is an excellent way to lower facility maintenance costs, as time can be utilized more efficiently and costly problems can be avoided. The lifespan of your equipment can also be extended thanks to regular maintenance—another key way to save money for your facility.
What Types of Maintenance Can Be Scheduled?
There are four primary types of maintenance: reactive maintenance, deferred maintenance, routine maintenance, and preventive maintenance.
- Reactive maintenance refers to maintenance and repairs that are performed after equipment has already broken down or suffered an error. The purpose of reactive maintenance is to restore equipment back to its normal operating condition. Emergency maintenance is a type of high-stake reactive maintenance that is done to prevent harm to people, property, or businesses.
- Deferred maintenance refers to any type of maintenance work that is delayed due to a lack of resources such as time, labor, or funding. The caveat with deferred maintenance is that while it is often done due to shortcomings in budget and/or labor, it can end up being even more costly over time if maintenance is delayed. Due to the nature of reactive and deferred maintenance, building out a maintenance schedule for either of these could prove difficult. On the other hand, scheduled maintenance goes hand-in-hand with routine maintenance and preventive maintenance.
- Routine maintenance includes all maintenance tasks that are performed on a regular basis. These activities can include regular inspections, machine services, and equipment checks. The primary objective of routine maintenance is to catch any potential issues before they have the chance to snowball into serious problems.
- Preventive maintenance is the regular maintenance of equipment and assets with the aim of reducing unplanned downtime and unexpected equipment failures. A solid preventive maintenance plan can reduce the amount of reactive maintenance required at your facility. Preventive maintenance can be divided into four categories: inspection, detection, correction, and prevention. Both of these types of maintenance require regular, consistent scheduling in order to be successful. As such, your facility’s maintenance schedule should include all routine and preventive maintenance tasks.
Creating a Maintenance Schedule
To engage in effective maintenance planning, follow these steps:
- Asset by asset, determine the regular maintenance tasks that will need to be performed. Include any standard operating procedures (SOPs) that your facility has established when applicable.
- Schedule the work. In this stage, bring together all of the maintenance tasks that need to be done and organize them in a way that doesn’t overload any particular department and doesn’t try to force too much work into a given time period.
- Assign workers and contractors to maintenance tasks that may require additional personnel to handle procedures. It’s very important here that you include estimated working hours so that everyone involved can plan accordingly.
- Include inventory and spare parts. This can create some leeway in your maintenance plan in the event that equipment or assets do break down.
- Be sure to highlight any specific permits or licenses that are needed by workers or contractors to operate equipment.
Following these steps will ensure that your maintenance schedule is clear and easy to follow, which will avoid confusion and increase efficiency.
How Do I Implement This?
At this point, you may be thinking, “That sounds good…but implementing maintenance scheduling also sounds like A LOT of work.” This can be especially true if you often find yourself already struggling to keep up with facility operations and chasing paper trails of work order requests and inventory checklists.
.jpeg)
The solution? An all-in-one facility management platform like FlowPath, of course! With FlowPath, you’re able to automate many of these processes—such as scheduling work orders, assigning maintenance tasks, and tracking inventory. By working in conjunction with an easy and helpful facility maintenance software, your team will be extremely well-equipped to take on scheduled maintenance tasks and avoid the stress, confusion, and fatigue of “old-school” facility maintenance.
FlowPath is the maintenance management software for the next generation of FMs. Say goodbye to manual processes and increase your facility’s efficiency and profitability in no time. Better processes mean smoother operations and a happier team. Adopt a facility management style that works for you.
Schedule a demo and see what the hype is all about.
FAQ
What is a maintenance schedule?
Scheduled maintenance is any maintenance task that takes place after a documented request, scheduling, and assignment process. A maintenance schedule is simply a built-out plan for completing said maintenance tasks.
What are the benefits of scheduled maintenance?
- Increased efficiency
- Reduced maintenance costs
- Greater asset life expectancy
- Increased workplace safety
- Higher worker satisfaction
What are the 4 types of maintenance?
The primary types of maintenance are reactive maintenance, deferred maintenance, routine maintenance, and preventive maintenance.