6 Ways to Manage Inventory Tracking | FlowPath
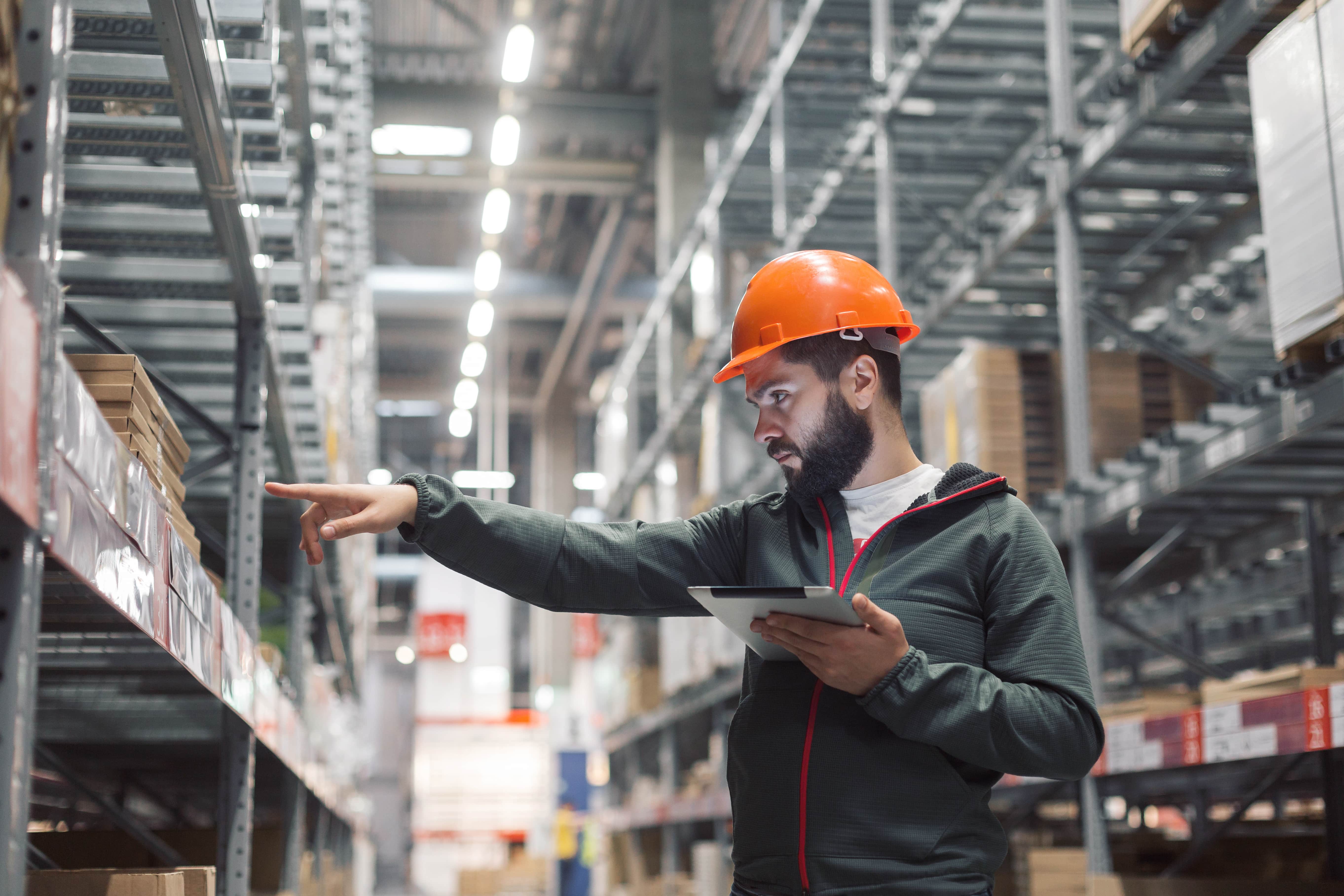
In recent years, the demand for inventory management software has more than doubled. Businesses and facilities everywhere recognize the need for easier, more efficient inventory tracking and parts management. Here’s the thing—many don’t know where to begin.
Have no fear.
Building an effective inventory tracking process isn’t as daunting a task as it seems. And, once you are able to streamline your asset maintenance, the result will be reduced costs, less performance interruptions, and increased overall productivity. Keep reading for the best tips on how you can improve inventory management at your facility.
Key Components of Effective Inventory Maintenance
To master inventory tracking at your facility, you need to consider a number of factors.
These include:
- Operational approach
- Work order standardization
- Effective spare parts management
- Clearly defined lead times for assets
- Calculated risk associated with equipment
- Secure processes and delegation of responsibilities
When all of these facets of inventory maintenance are taken into account and executed correctly, facilities are able to operate at their maximum potential, ultimately leading to higher returns and less stress along the way. Let’s take a look at each of these in more depth.
Operational Approach
Facility operations usually fall under one of two categories. The first strategy is taking a reactive approach. This involves creating operational plans based on responding to events, including problems that may arise from seemingly nowhere. Let’s face it: things happen. Mistakes are made. So completely abandoning reactive approaches isn’t a totally viable option. Still, there is a more effective way to mitigate these responsive events by taking another approach.
Enter the predictive approach. Inventory tracking is a great way for facilities to stay ahead of responsive events and even avert future problems before they have the chance to happen. And this relationship goes both ways, like a feedback loop. Predictive strategizing will only make inventory maintenance easier. Collecting and analyzing data, highlighting failure patterns, and predictive outlooks of the future can all do wonders for your facility’s inventory tracking process.
Work Order Standardization
A formulated and straightforward work order process can be pivotal in improving inventory tracking. Your work order process should be easy to follow and standardized for all employees. One example of how you can achieve this is through workflow automation.
Automating work orders ensures consistency in procedures and also creates a readily available log of what needs to get done and when. This can inform facility managers what assets will be needed in the near future, making spare parts management that much easier. And whether inventory tracking is automated or not, the time and resources saved by standardizing work order processes will give facilities more resources to devote to refining their asset maintenance.
Effctive Spare Parts Management
Accurate tracking of spare parts is key to inventory control. This can be done by establishing a clear check-out system to signify when a part is taken from stock and put into operation. Inventory tracking can also be streamlined by developing a clear set of criteria for defining and categorizing inventory assets, such as designating parts as in use, primary replacements/substitutes, and spares.
Implementing regular inventory status checks can also reduce excess stock and lower the cost of inventory maintenance. This can be done in one of two ways:
- Periodic inventory management means taking inventory at designated times, such as monthly, quarterly, or annually.
- Perpetual inventory management, which aims to track stock levels on a transaction-by-transaction basis.
Your process will likely depend on the type of business you run and the unique needs your facility has.
Clearly Defined Lead Times for Assets
Having a thorough understanding of lead times for different spare parts is an essential part of effective inventory tracking. This informs facility managers when making decisions over which parts need to be ordered and what volume of each needs to be ordered. Parts that are not critical for everyday operations lend themselves to more flexibility when it comes to lead times. On the other hand, assets that are needed for day-to-day procedures need to be closely tracked to ensure proper parts management. Even a day or two without them can potentially lead to hefty financial losses.
For holistic inventory tracking, one solution is creating a list (or lists, if they can be broken up) of all spare parts with their respective estimated shipping and processing times. This can be subsidized with a list of alternative brands or parts that can be used in the case that the desired assets are not readily available. In responsive situations, this could come in handy. You can also automate this process (with a tool like FlowPath) to prevent the clutter of computer files or physical paper lists.
Calculated Risk Associated With Equipment
Knock on wood, but the reality is that any of your facility’s equipment can fail at any time. Because of this, it is vital when keeping up with asset maintenance that you consider the risk and calculate the estimated downtime associated with any equipment failures that could arise.
This can be as simple as estimating the total cost incurred by one hour of downtime. Lead times for parts also play into this. Additionally, consider the cost of purchasing “new” vs “used” parts for replacements, especially when trying to optimize your budget.
Secure Processes and Delegation of Responsibilities
Defining who is responsible for what parts of inventory is essential for effective inventory tracking. If everyone has access to inventory (whether that’s digitally or physically in a warehouse), you’re likely to experience inventory inaccuracies. You can avoid this by restricting access to certain parts inventories, giving only specific staff members the ability to access them and record changes. And, ensuring your CMMS software has the ability to support such restrictions will be a key consideration for new facility management tool adoption.
Because parts management systems are so essential for accurate inventory tracking, security considerations are also significant here. Security measures can include physical measures such as parts counters and security cameras, as well as digital barriers, like gated access to inventory maintenance software that requires an admin username and password.
Enhance Your Inventory Tracking Today
All of the aforementioned components of inventory maintenance are important considerations for facility managers who want to refine their inventory tracking procedures. In order to implement these processes into your facility’s workflows, you’ll need a platform where your inventory tracking tools can live.
FlowPath can do the job.
.jpeg)
Not only does our software help with procurement and management of inventory, but it’s also equipped to streamline your other facility processes. From work order management to project planning to reporting, FlowPath offers all that and more in a user-friendly interface.
Schedule a demo today to discover what FlowPath can do for your facility.